How can companies design their cleanrooms in order to reach the air change rates required by ISO? Words by Simplex's Jerry Cross
Whatever the cleanroom’s function, contamination must be stringently controlled and particulates removed effectively. Vertical Clean Bench
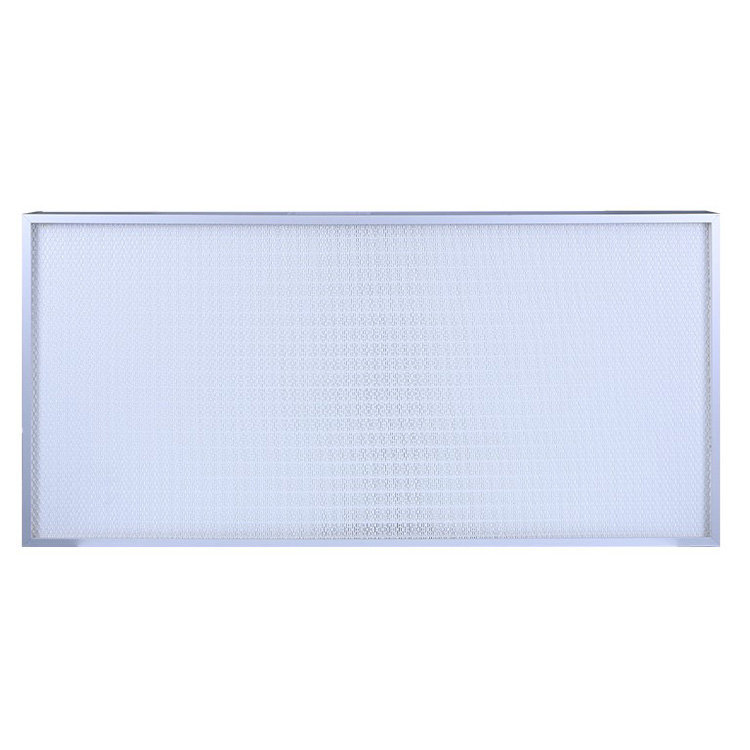
While in the past, a variety of benchmarks, standards and outdated documentation have been used to statement a base-level requirement, we now have ISO standards that are dedicated to cleanrooms.
These outline the practices and procedures required to manage the risk of contamination and take context into account, such as ceiling height and directional flow. And as an international standard, this means that all cleanrooms that adhere to ISO requirements can be certified to be of the same regulated level, providing a reliable and consistent standard across the world.
In this article, we look at how companies can design their cleanrooms in order to reach the air change rates required by ISO. And how Simplex Modular Cleanrooms and Separation Systems by Subzero Engineering are engineered to optimise and protect your mission-critical environments.
There are nine levels of ISO regulated cleanrooms, with Class 1 being the cleanest. With regard to ISO 146144-4 standards, air changes per hour refers to the number of times per hour the air in a cleanroom is replaced with clean, filtered, and treated air. The measurement of contamination is calculated by “parts-per-cubic-meter”; dividing the volume of air sent into the cleanroom as a unit of time by the total volume of the cleanroom.
ISO Class 9 through ISO Class 6 rooms are determined based on air changes per hour, whereas ISO Class 5 through ISO Class 1 rooms are based on the flow of air through the room in metres per second.
The ISO 1 specification for cleanrooms requires less than two particles greater than 0.3 microns and no particles greater than 1.0 microns per cubic metre.
The total rate, flow pattern, and exchange efficiency often have direct and indirect implication
ISO 8 cleanrooms are required to have 20 air changes per hour of HEPA-filtered air and less than 29,300 particles/cubic metre greater or equal to five microns. By comparison, a non-cleanroom such as an air-conditioned office space would have more than 10 times as many particles per metre. On average, Simplex cleanrooms are rated at ISO 7.
In order to achieve the rating required you need to ask yourself if you’re moving the contaminated air out of the area properly. It’s relatively easy to clean the air, but you need to work out how the air is getting into and out of the space.
The majority of cleanrooms are positive-pressure rooms. Air is introduced into the cleanroom, typically at the ceiling level, after passing through a fan-powered HEPA filter that removes particles as small as 0.5 microns. This creates a pressurised room in which the air pressure in the room is greater than outside the room. The air, and the contaminants in the air, are then pushed down towards the floors and ultimately pushed out via vents low in the walls of the room.
This means that air and contaminants from the processes in the room are constantly flowing out of the room. In addition, the air exiting the room, either through vents or when doors are opened, is at a pressure that is sufficient enough to prevent contaminants from entering via those openings.
Negative-pressure rooms are designed to keep contaminants from leaving the room. A negative pressure room can be used in cases of infectious diseases and pathogens, bio-contaminants and hazardous processes using chemicals, flammables and potentially explosive liquids and powders. In this case, the concern is not what gets into the room, but what gets out of it.
In a negative pressure room, the air is pulled out of the enclosure through reversed HEPA filters or low wall returns. This creates negative pressure, while air is constantly being drawn in through venting and other openings. The force of the air entering the room prevents contaminants from escaping.
Achieving a cleaner class of cleanroom is all about airflow. It’s a matter of bringing clean air in through HEPA filters in the ceiling and moving contaminated air out through vents in the walls or floors. Therefore the greater the number of HEPA filters and vents, the greater the air change rate.
Air change rates determine the design and performance criteria for a cleanroom HVAC system. The total rate, flow pattern, and exchange efficiency often have direct and indirect implications on cleanroom performance and cost which, in turn, determines the rate-of-return on investment for a cleanroom.
Cleanrooms are measured at three different levels: As Built, At Rest and Operational
Simplex typically designs cleanrooms rated at ISO 7 level. This means 70/75 air changes per hour. Taking the cubic foot of the room, Simplex multiplies the room size by the changes per hour that are required and then divides it by the cubic feet per minute (CFM) that the HEPAs are pulling out. Simplex typically designs for 650CFM HEPAs, which is a standard 2 x 4 HEPA used in most applications.
However, if you used a room side replaceable HEPA, there will be a maximum airflow of approximately 550CFM. Some high-efficiency high-output HEPAs can produce 900CFM, meaning not as many are required. Fan filter units with higher CFM output can help extend the life of your HEPA filter and can also be used when greater airflow is required in areas with limited space.
Cleanrooms are measured for the particulate count at three different levels: As Built, At Rest and Operational.
As Built refers to the cleanroom as it is when it is built, empty of any equipment, materials or workers. As Built is normally used when a cleanroom is first constructed.
At Rest refers to the cleanroom once equipment, machinery, furniture and product have been moved in, but before any workers. All these elements bring with them sources of contamination and change of airflow direction. There is always an expected change in particulate count when At Rest.
The Operational level refers to the cleanroom when all the equipment and materials are moved in and there are workers in the room performing tasks and physically moving around the room. At the Operational level, you would expect to see far higher particular counts as human beings are considered the biggest contaminant of all. Skin particles, hair and other physical detritus are very much to blame.
In this case, gowning, cleaning, type of equipment and the workflow process can all affect contamination. This is the most challenging of all ratings when trying to assess air change rate requirements as most constructors are not fully aware of the operational usage.
Cleanrooms are typically certified by Simplex as to their level of cleanliness at the As Built level. However, a recent project where a client wanted ISO 5 at Operational rating meant Simplex added a lot more airflow to meet those unseen processes. In this case, Simplex designed the cleanroom for ISO 4 in order to achieve ISO 5.
With so many generators of contaminants to consider, such as operational equipment, people or even just a desk that’s in the way of airflow, it may be considered that building sections, or cleanrooms within the cleanroom, could be a better option. A cleanroom with a modular design allows the cleanroom to be used as you require, expanded or altered without having to be rebuilt from scratch or having to discard part or all of your original investment.
Every cleanroom that’s ISO Class 7 or cleaner, should have an anteroom for gowning, set off from the larger cleanroom. At the very least, this keeps street dirt from getting into the clean area. Interior isolation is also important in food processing and pharmaceuticals to prevent cross-contamination. A recent Simplex project called for dividers for a vitamin processing operation. In this case, if vitamin B12 managed to navigate its way into the Vitamin C work area, that’s cross-contamination, meaning manufacturing shutdowns, product recalls and lost profits.
Maintaining air change rates is relatively simple by adjusting the airflow as your operation requires. As you're certifying a room, you can tell when the airflow is dropping, or you're losing air changes for particulates in the air with less air changes. Therefore, you need to expand or improve the HEPA filters. Producing more CFM gives you the ability to make your filters last longer and to retain the level of the ISO standard you’re aiming for.
Producing more CFM gives you the ability to make your filters last longer
There is a difference between single-pass and recirculating rooms. A single-pass room is a simple design in which air is pumped into the room from the top and blown out vents at the bottom. If you have air-conditioning in your cleanroom, then you don’t want to just blow that expensive air-conditioned air through the cleanroom and out into a warehouse or other environment where it does little good.
A recirculating design uses a double-ceiling system or a double wall, or a combination of them both. Cooled, clean air is introduced through the HEPA filters. Then it flows out of the room, carrying with it any contaminants, into either the air chase or the ceiling plenum, and reintroduced into the room after once again passing through the HEPA filters.
We believe that going forward, manufacturers are going to have to start to prove their airflow. Simplex has recently launched a CFD analysis program to prove and ascertain that it is unidirectional airflow and that it's going to meet the client’s requirements.
CFD modelling assists in designing efficient technology solutions for new and legacy data centre environments by providing predictive results that bridge high-performance computer server operations with the critical mechanical system. Subzero Engineering now includes CFD services for Simplex cleanrooms.
It improves overall energy efficiency (Lower PUE) which easily identifies and eliminates hot spots, determining the right airflow strategy and validating the design.
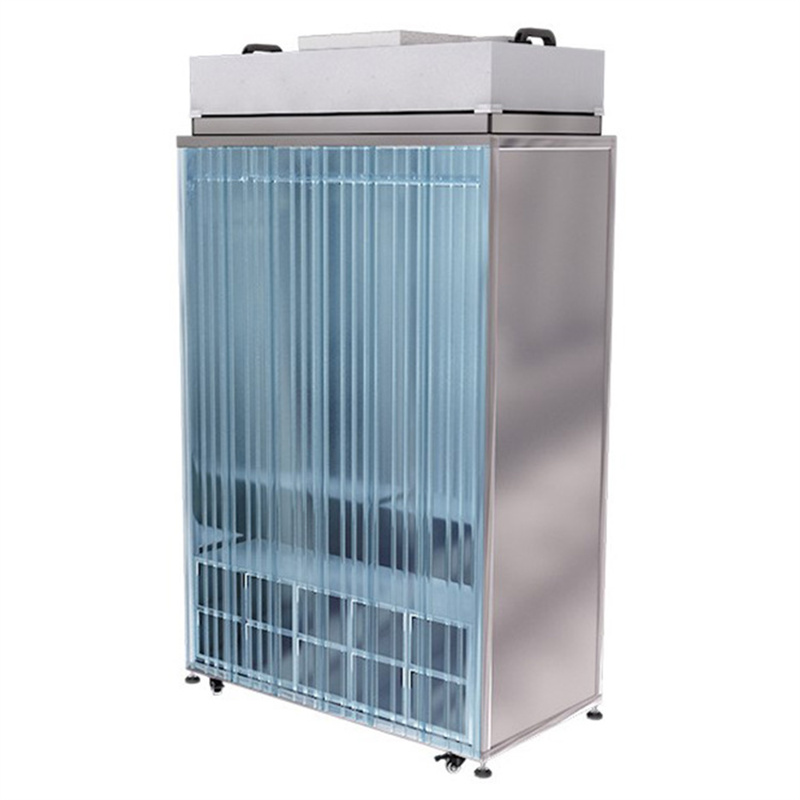
Clean Room Material Levelling the playing field for everybody, the ISO rating keeps the level of cleanrooms consistent across industries. Cleanrooms used to be regulated under a federal standard, which meant the US were able to design a cleanroom one way with certain levels of standards, while the European market could design differently. This international standard has been built for all, ensuring consistency, reliability and of course efficiency across the board, across the globe.